What are silver streaks?
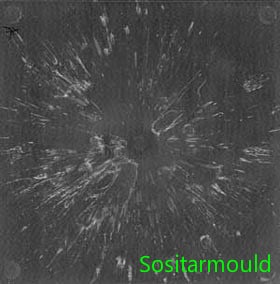
Silver marks / silver streaks are splatter marks on product surface which are caused by the volatilization of air and moisture contained in the plastic material, or the decomposition and burning of mixed dissimilar plastics. Usually, they radiate outward in a fan-shaped manner from the gate location.
Many plastic materials absorb a lot of moisture during storage. So, if they are not fully dried before injection molding, the residual water will be converted into water vapor during the plastic injection molding process, thus accordingly causing splatter marks on product surface.
In addition, in the plasticizing stage of the raw plastic material, a certain amount of air is often trapped in the melt. If this amount of air cannot be successfully vented during the plastic injection molding process, silver streaks will also be generated on product surface. Moreover, some cracked or burnt plastics will also lead to silver streaks on product surface. See the figure for silver streaks:
Cause Analysis of Silver Streaks
(1). The melt contains volatile matter
The most commonly seen form of the silver streak is the needle-like silver-white stripes caused by elongated flat bubbles, of which the main types include degradation caused silver streaks and water vapor caused silver streaks.
All types of silver streaks are generated by the volatiles precipitated from the melt front. For example, the degradation caused silver streaks are small bubbles that are formed and distributed on the surface of plastic products when partial thermoplastic degrades and gas decomposes after being heated. Usually, the marks left by these small bubbles on plastic product surface are arranged in a “V” pattern, of which the tip faces away from the center of the gate. Another example is that the main cause of the water vapor related silver streaks is that the water content in the raw material is too high, wherein the bubbles generated when the water volatilizes cause the surface of the plastic product to produce silver streaks, especially true for the super absorbent resins such as PA and HIPS. If the vapor generated by the volatilization of water in the molten plastic cannot be completely vented, the water vapor caused silver streaks will be produced on the surface of a plastic product.
To eliminate silver streaks, we should start from the following three aspects:
First of all, with regard to raw material selection and processing, to deal with degradation caused silver streaks, it is necessary to select resins with a uniform pellet size as much as possible, screen out the powder in the raw material, reduce the amount of recycled materials, and remove the residual foreign materials in the barrel; for water vapor caused silver streaks, the raw material must be fully dried according to the requirements of the resin.
Second, when it comes to processing and operation, to deal with degradation caused silver streaks, it is necessary to lower the temperature of the barrel and the nozzle, reduce the residence time of the melt in the barrel, prevent local overheating of the melt, and slow down the screw speed and forward speed to shorten the pressurization time; for the water vapor caused silver streaks, the backpressure and screw compression ratio should be increased, while the screw speed should be reduced or venting screw applied.
Third, in aspects of mold design and operation, to deal with degradation caused silver streaks, the sections of the gate, the sprue and the runner, as well as the cold slug well should be increased, so as to improve the venting conditions of the mold. For the water vapor caused silver streaks, the mold venting holes should be increased or vacuum vents should be adopted, to minimize the gas remaining in the molten plastic, while checking whether the mold cooling channel is leaking, so as to prevent the mold surface from frost and moisture caused by overcooling. If the mold surface is moist, there will be traces of silver streaks on the surface of the plastic product.
Besides, during the plastic injection molding process, the mold release agent will also generate a small amount of volatile gas, so their usage should be minimized, and the ejection resistance can also be reduced by improving the surface finish of the mold cavity.
(2). Poor melt plasticization
If the melt is not fully heated and plasticized in the barrel, streaks will be produced when the incompletely melted material is exposed on the surface of the plastic product. These dark specks are shaped like mica flakes, each with the size close to that of a material pellet. When observed under transmitted light, the product has poor transparency at the specks, and sometimes the convex unmelted raw material pellets can be clearly seen.
Based on the cause of the dark specks, to solve this defect, the barrel temperature should be appropriately increased and the molding cycle appropriately extended. We should try to apply the internal heating sprue, or increase the size of the cold slug well and the runner. When possible, a plastic injection molding machine with a relatively large barrel can also be used to improve the plasticization of the melt.
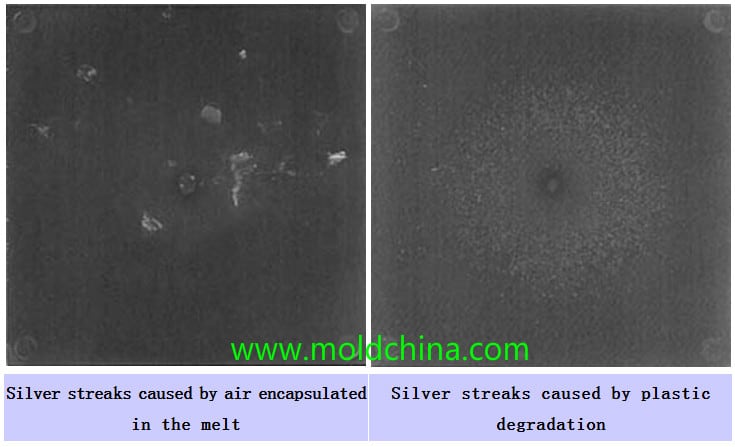
Silver Streak Analysis & Troubleshooting
(1). The moisture and volatile content in the raw material is too high.
The raw material should be pre-dried.
(2). Poor mold venting. Vents should be increased to improve the venting
performance of the mold.
(3). Poor contact between the nozzle and the mold. The location and geometric
size of the two should be adjusted.
(4). When silver streaks always appear in certain locations, we should check
the corresponding cavity surface for surface damages / scars. If so, the scars on
the cavity surface should be removed by machining.
(5). When different types of resins are mixed, silver streaks are prone to
occur, so mixing of dissimilar resins should be avoided.
Silver Streaks
Silver streaks are a microcrack defect caused by high polymer under the action of solvent, ultraviolet light, mechanical force and internal stress, which shows a silver-white luster under light irradiation, with a length of up to 100μm, and a thickness of about 1-10nm. It is composed of the silver streak substance (highly oriented polymer microfibers) and hollows – the silver streak substances link up the sides of silver streaks in the hollows. The diameter of the large microfiber is about 20-30nm, and that of the smaller ones is about 10nm. The hollow accounts for about 40%-50% of the volume of silver streaks. The silver streak substance features certain mechanical strength and viscoelasticity, so that it is able to bear a certain level of load, while can also disappear by itself above the glass transition temperature, which is referred to as self-healing.
Silver streaks are very similar to cracks. The difference is that the crack is empty inside, but the hollows in silver streaks are connected by the silver streak substance. When the silver streak thickens, and the silver streak substance breaks, it will become a crack. The appearance and development of silver streaks cause the mechanical properties of the raw material to deteriorate rapidly. After a plastic product is molded, if silver streaks appear in the direction of the melt flow, it means the raw material pellets are insufficiently dried or the thermal stability of the material is not strong enough during the plastic injection molding process. Resistance to silver streaks is the ability of plastics to resist the appearance and increase of silver streaks, which is one of the important performance indicators of plastic materials.