What is gate?what types of gates do we use?
Injection molding gate is the last opening that allows the molten plastic to flow into the cavities ,the most common gate types in injection molding include:Side gate/edge gate,Tab gate,Fan gate,Sub gate,Ring gate,Direct gate/sprue gate,Banana gate,Pin point gate,Hot runner(Point gate,Valve gate)
Injection molding gate design and location selection
a. Not allowed to affect product appearance;
b. Try to keep a consistent distance to each part of the cavity;
c. The gate should be faced with the wide part of the cavity, easy for shrinkage compensation and melt flow;
d. Avoid direct injection on pins, or direct impact on weak inserts;
e. Minimize welding marks, or only allow welding marks on less important surfaces or strong enough parts of the product.
f. Selection of gate location should be conducive to mold venting;
g. The gate should be easy to remove.
Side Gate/Edge gate
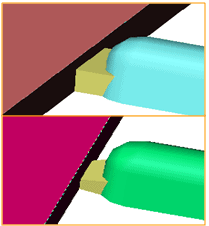
Pros: 1. Simple shape and easy processing
2. Easier to remove the gate
Cons: 1. The plastic part and the gate cannot be separated automatically
2. Gate marks are easily generate on the plastic part
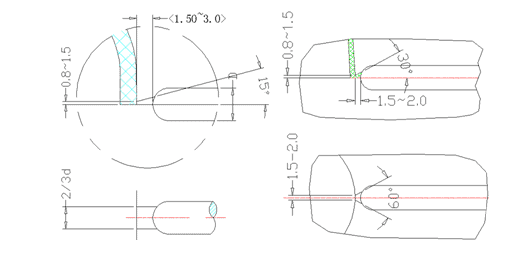
Tab Gate
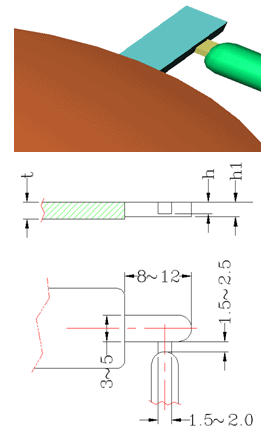
Pros:
1). When the melt flow hits the tab wall, the flow velocity is reduced and flow direction changed, allowing it to enter the cavity evenly and smoothly at the tab wall.
2). Help improve air streaks around the gate.
Cons:
1). The gate needs to be removed manually;
2). Obvious gate marks are generated on the edge of the plastic part.
Applications: Usually used for flat parts made of highly transparent plastics, such as PC and PMMA.
Fan Gate
Suitable for flat, shell or box products
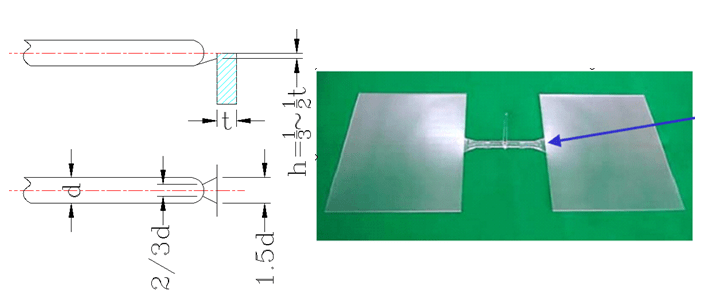
Ring Gate
Prevent welding marks;
Able to evenly fill cylinder-shaped products;
The cross-sectional area of the ring gate is quite large, so difficult to remove;
Other gates include claw gate and spoke gate
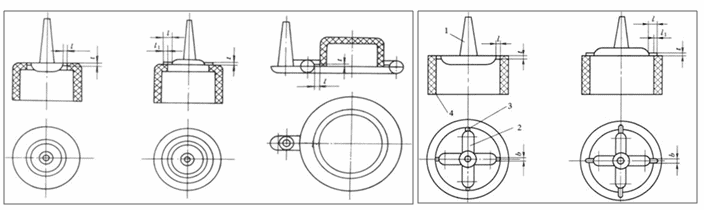
Pin Point Gate
Usually used in three-plate mold and runnerless mold
Pros:
1). A greater degree of freedom for location selection;
2). The gate falls off automatically, hardly leaving any marks;
3). Very suitable for barrel-shaped, shell-shaped, box-shaped and large flat plastic parts;
4). Low residual stress around the gate
Cons:
1). High injection pressure loss;
2). Complicated mold structure.
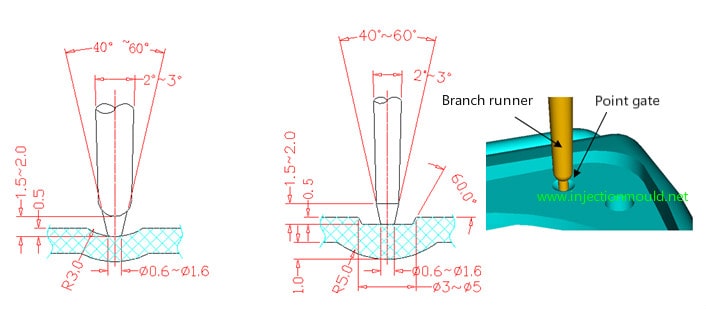
Sub Gate
Pros:
1). Flexible location selection;
2). The gate falls off automatically;
3). Able to be designed on either the core or the cavity.
Cons:
Not suitable for elastic plastics
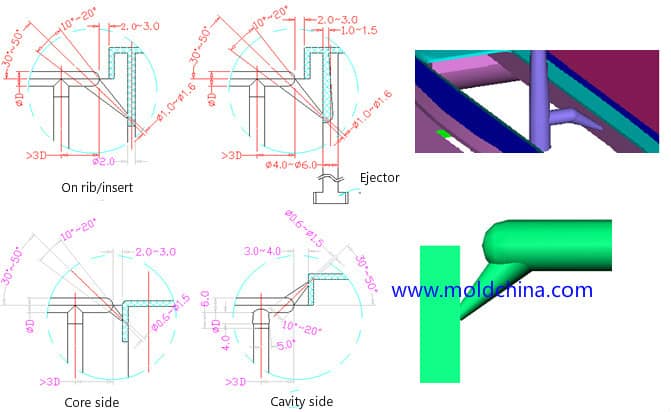
Banana Gate
Pros:
1). Gate and parts are separated automatically;
2). No additional treatment is required for the gate location;
3). No gate marks will be generated on product surface.
Cons:
1). There may be shadow marks on product surface;
2). Complicated processing;
3). Easy to break and block the gate if inappropriately designed.
Applications: Commonly used for ABS, HIPS. Not suitable for crystalline materials, such as POM and PBT, nor rigid materials, such as PC and PMMA.
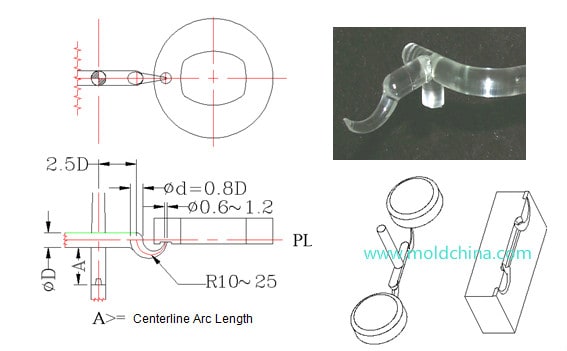
Direct Gate
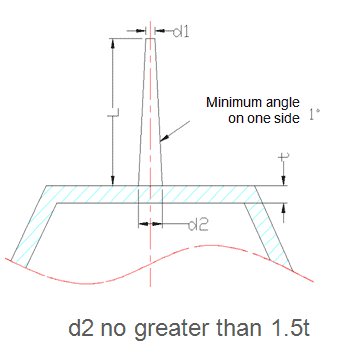
Pros:
1). Low pressure loss;
2). Simple production;
Cons:
1) Relatively high stress around the gate
2) Gate (runner) needs to be removed manually;
3) Obvious gate marks on product surface;
Applications: Used for large and deep barrel-shaped plastic parts;