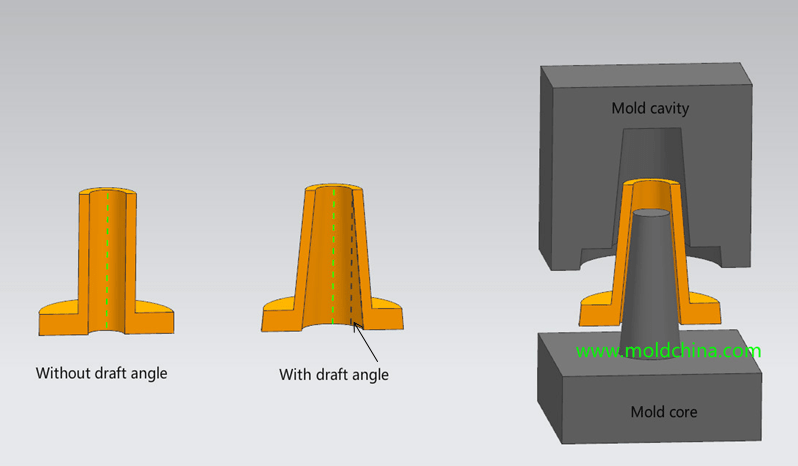
As the plastic material cools and shrinks, a plastic product is tightly wrapped around the mold core. In order to facilitate product release, an appropriate draft angle should be designed on the product surface that’s parallel to the release direction. The so-called draft angle refers to the inclination angle that should be designed on the plastic part surface parallel to the direction of mold release, calculated as a degree measurement. The draft angle of a plastic product depends on its shape and wall thickness, as well as the shrinkage of the plastic material. If the angle is too small, it’ll be difficult to release the product, causing the surface of the product to be damaged or cracked; but if the angle is too large, dimensional accuracy of the plastic product will be affected.
Characteristics of the draft angle
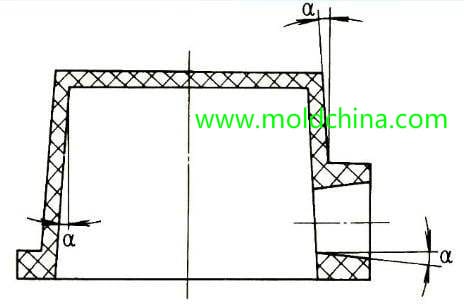
1) Facilitate mold release. The main function of the draft angle is to facilitate product release. After a plastic product is molded in the cavity, the plastic part tightly wraps around the convex parts in the core or cavity due to plastic shrinkage, which makes it difficult to release the product. With a draft angle in place, the plastic product can be easily separated from the mold cavity.
2) Guarantee the surface quality of the plastic product. After a product is molded, it will tightly stick to the cavity surface. If an ejector mechanism is used to forcefully release the mold, this strong external force will inevitably cause burrs or scratches to product surface, thus impacting the surface quality of the plastic product.
Draft angle design considerations
1) The higher the precision of a plastic product, the smaller the draft angle should be, so as to obtain a high-precision plastic product; for the large size plastic products, the draft angle can be designed smaller because of the easier mold release.
2) For plastic parts made of glass fiber reinforced plastics, a larger draft angle should be designed due to the larger friction.
3) If the plastic contains a lubricant, release of this plastic product will be easier, so a smaller draft angle should be designed.
4) For plastic parts with complex shapes, mold release is usually very difficult, so a larger draft angle should be designed.
5) For plastic materials with great shrinkage, its adhesion to the mold cavity is rather strong, so a larger draft angle has to be selected.
6) As for the direction of the inclination, the inner hole is based on the small end, and meets the dimensional requirements in the drawing, and the angle is obtained towards the direction of the larger end. The shape is based on the large end and meets the requirements in the drawing, and the angle is obtained towards the a smaller end.
7) Usually, the draft angle is not limited by the tolerance zone of a plastic product, but the draft angle of a high-precision plastic part should be kept within the tolerance zone.
8) When the surface roughness of the core is small, the polishing direction is consistent with that of mold release, the friction between the part and the mold materials is low, the plastic molding shrinkage is small and the plastic part is sufficiently rigid, mold release will be easier, so the draft angle can take the smaller value, and on the contrary, take the larger value.
9) Different types of plastic materials should have different draft angles. The table shows the draft angles recommended for different plastics.
10) If there are inclinations on both the inside and the outside of a plastic product, and the product needs to be attached on the core, the inclination on the inner surface should be smaller than that on the outer surface, or even design the inner surface without an inclination or increase the draft angle of the cavity.
11) If a plastic part is designed with several holes along the mold release direction or follows a rectangular grid pattern, which increases the release resistance, an inclination of 4-5° should be designed; when the side wall is designed with a leather pattern, a slope of 4-6° should be adopted. Generally speaking, as long as the inclination does not impede the use of the plastic part, the angle value can be made larger.
13) For a plastic product with a deep cavity, not only the inner and outer surfaces need to be designed with a sufficient inclination angle, but also the inclination of the inner wall surface is required to be greater than that of the outer wall surface, so as to ensure the density at the bottom, as shown in the figure.
14) A plastic product is usually designed with a boss when it is inserted, or used for connection. In order to facilitate mold release, the boss must be designed with an inclination angle usually of 1-2°.
15) For box and cover plastic products, the inclination angle is dependent on the height of the products. When the height < 50mm, the inclination angle, a = 1.6-2.0°