Plastic injection mold is used to give shape to molten plastics via the process of injection. Designed as a hollow steel block with cavities. there are multiple holes made inside the mold to realize temperature control by way of oil, water or heaters.
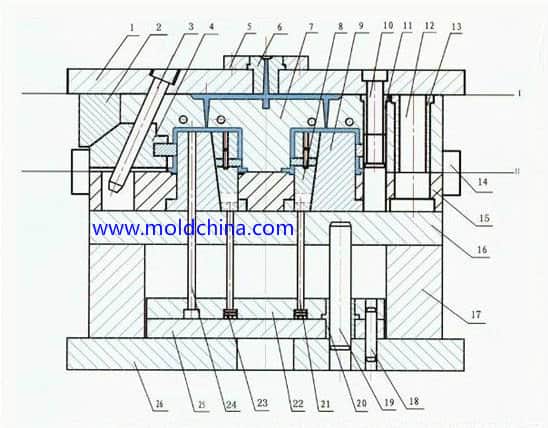
The basic structure of plastic injection mold
The five systems of plastic injection mold: Gating system, Guidance system, Molding system, Ejection system, Cooling system
- Gating System:
Sprue: Where the molten plastic flows through from the injection machine to the mold.
Runner: Where the molten plastic flows through before reaching different cavities.
Gate: The last opening that allows the molten plastic to flow into the cavities.
Cold Slug Well: When the molten plastic flows in the sprue and runner, it will solidify due to heat transfer with the mold. The cold slug well is where the solidified material is stored before entering the cavities.
Venting: 1. Expel air from the mold cavity during the injection process of the molten plastic ; 2. Get rid of the various gases produced during injection molding processing.
- Guidance System:
In-mold opening/closing process, mold displacement will occur due to manufacturing tolerances and installation tolerances. When the mold is closing, it is required that the mold can return to its original position. This is where guidance and location (i.e. mold guidance system) fit in.
- Molding System:
Molding System: A closed space that consists of the core, cavity, and inserts, etc.
- Ejection System:
The ejecting system include the ejector pins, ejector blocks, ejector sleeve and lifters, etc. to push the injection molded parts away from the core or the cavity after cooling.
- Cooling System:
The mold itself is a large cooling system. To achieve a better cooling effect, one or more groups of cooling channels will be designed for the mold. Usually, the distance between the cooling channel and the product is twice the diameter of the channel. The coolant is not necessarily cold water – it can be water at 100 degrees Celsius depending on the mold temperature and sometimes it can also be hot oil..
Which material(steel) are used for plastic injection mold?
Mold life above 0.5 million: the steel choices include Swedish brand 8407 and S136; American brand 420 and H13; European steel 1.2316, 1.2344 and 1.2083 and Japanese brand SKD61. For strongly corrosive plastics, S136, 2316 and 420 steels are normally chosen.low corrosion plastics can also choose SKD61, NAK80, PAK90 and 718M steels. S136, 2316, 718S, NAK80, PAK90 and 420 steel materials are suitable for transparent and mirror polishing products, while highly transparent products should primarily select the S136, and secondarily the 420 steel materials.
Mold lifer between 0.3 million and 0.5 million: Mostly use pre-hardened steels, such as S136H, 2316H, 718H, with a hardness ranging from HRC 32 to HRC42.
Mold lifte less than 0.3 million: Usually use the P20, 718, 738, 618, 2311 and 2711 steel materials. For molds with extremely low requirements, S50C and 45# steels may be used
The basic types of plastic injection mold
Two plate mold: When the mold opens, the cavity and the core are separated to release the molded product. as a two plate mold . Being most widely used, it is the simplest and most basic form of the injection mold, and can be designed as a single-cavity or a multi-cavity injection mold.
Three plate mold: It adds a partially movable intermediate plate (also called a movable runner plate, on which the gate, runner, as well as other parts and components required for the core are designed) into the fixed mold half. When the mold opens, the runner plate is separated from the core plate for a fixed distance , so that the sprue and runner can be removed from between the two plates.
Hot Runner Mold : A runner-less injection mold refers to the mold which employs adiabatic heating to heat the runners and keep the plastic material between the cavity and the injection nozzle in a molten state, so no sprue or runner are generated when the mold opens to eject out the injection molded product.
The standard & brand for mold base & components:
Mold Base: EMP, DME, HASCO, FUTABA, LKM.
Hot Runner: MOULD MASTER, SYNVENTIVE, HASCO, DME, YUDO, INCOE
Latch Lock: DAIDO, HASCO, STRACK, RABOURDIN
Standard components: DME, HASCO, LKM, HEB, STRACK, OPITZ
Mold design
Plastic injection mold design is started with a 2d drawing layout, basic mold spec. will be drawn out, such as mold size, gating type, parting line location, ejection method, cavities layout, mechanical design, accessories used, steel types of each component used, etc.
Full 3D design in detail and NC programming will follow after the 2d design is approved by the customer or management. Depends on the complexity, The whole mold design process would need 3-7 days. Some of the complex molds require mold flow analysis to simulate injetion molding processs or several updates as per feedback from the customer, it could take much more time.
Plastic injection mold manufacturers must consider how to reduce the mold cost while ensuring high efficiency in production . How can we achieve this target? When designing a plastic injection mold, the following factors need to be taken into consideration:
Injection Molding Cost: Determine product arrangement and the number of cavities according to the size of the machine and the cost of each shot. The larger the number of products ejected, the lower the injection molding cost, because in the plastic injection molding process, the machine cost is calculated by the number of shots.
Appearance requirement: Determine the parting line according to the appearance requirements of a product. The location of the parting line has to facilitate mold processing, venting and mold release, etc. The more cavities, the more likely for appearance problems to occur.
Gate Type: Determine the shape, size and venting orientation of the sprue and runners. Hot runner molds cost a lot but save on runner material and improve efficiency.of course each type has its own advantages and disadvantages,It is up to the user decides.
Mold Release: Determine the ejection method and the placement of ejection system. Ejection system include ejector pins,ejector blade,ejector sleeve,ejector block and lifter.
Plastic injection mold design also involves the considerations on plastic material shrinkage and cycle time, as well as the determination of the cooling/heating method and the placement of the cooling channel. In addition, consider the service life of the mold, determine the steel hardness,thickness, size and processing difficulty.
Moldflow analysis
Moldflow analysis is the plastic injection molding simulation software that obtains data and results through the computer-aided to simulate the plastic injection molding process, based on which, the feasibility of the mold solution is to be evaluated, in a bid to improve mold designs.
The software we use:
Our engineer mainly used the following software:
Pro/ENGINEER
SolidWorks
AutoCAD
Moldflow
MasterCAM
Unigraphics
Animatronic
Surfcam
CATIA
The whole process of plastic injection mold manufacturing
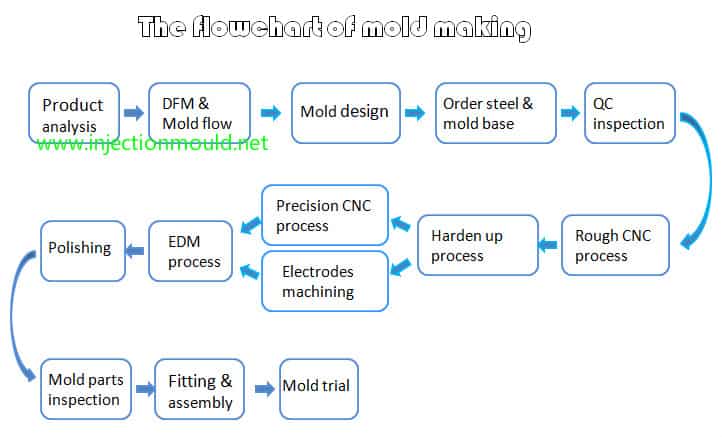