In recent years, as the mold industry of China continues to grow and upgrade, the level of mold design has been witnessing constant improvement. In the design of plastic injection molds for digital cameras, cell phones, home appliances, computer peripherals and laptops, the application of insert is gaining greater and greater importance. In the following article, we are going to describe the design of mold inserts from three aspects.
1. Characteristics of mold inserts
1.1. Pros of inserts
(1). Convenient for mold modification. As is known to all, the product designed by product development and design engineers are often revised. In such circumstances, an insert can be added to the to-be modified mold in advance, so that only the insert needs to be replaced when the mold needs to be changed in the future. And even, several more inserts can be designed for future replacement when the mold is being developed, thus making it easy to modify the mold without affecting efficiency.
(2). The addition of multiple inserts is conducive to mold venting, a very important indicator of mold performance. Generally speaking, inserts can often be added where the mold needs to be vented, so as to facilitate mold venting in combination with mold gaps or clearances.
(3). Convenient for mold machining. It is clear to us that there are some deep grooves in an injection mold, which make it very difficult for mold processing, polishing, filling and ejection. However, adding inserts in these locations is able to reduce machining difficulty.
(4). The design of the insert helps avoid EDM, thereby reducing processing costs.
(5).The addition of insert is able to stagger procedure, facilitate scheduling and improve efficiency.
(6). Increase the service life of a mold. Under normal circumstances, an insert is often added where the mold is easily damaged. Once the insert is damaged, it can be replaced, thus extending the service life of the mold.
1.2. Cons of inserts
(1). Increase the difficulty of mold assembly;
(2). Flashing is easily caused around the insert;
(3). Sometimes, the insert structure increases mold design and machining expenses, thus increasing production costs;
(4). Too many insert structures affect the design of mold cooling channel;
(5). Too many insert structures affect the strength of mold core.
2. Insert design
(1). Design mold core and cavity into inserts (as shown in Fig. 1). In this way, it is convenient to replace the core and cavity. This insert form is adopted when producing a small quantity of injection molded products, or when there are higher requirements on the strength of mold core and cavity.

(2). Design of shut-off and kiss-off inserts (Figure 2). During the mold design process, we will encounter some special holes that require the kiss-off or shut-off design. At this point of time, we need to use inserts.
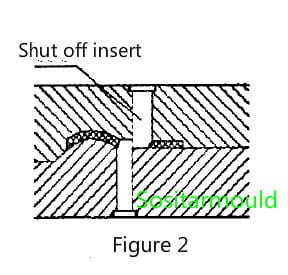
(3). In the design of slider, inserts are often used to reduce machining difficulty and facilitate the replacement of wear parts, but such a design reduces the strength of the slider.Therefore, it is applicablein occasions when there are lowerrequirements on slider strength (see Fig. 3).

(4). Similarly, with regard to lifter design, if the mold is used more than a certain number of times, the molding part of the lifter is also easy to wear. Then, to reduce cost and extend the service life ofthe mold, you can also consider using aninsert to solve theissue (Fig. 4).
(5). The venting design of a plastic injection mold is of great importance. To facilitate moldventing, you can also add an insert where venting is required (see Fig. 5). In a nutshell, the above-mentioned inserts are commonly used ones in the design process. In the actual design process of a plastic injection mold, the form of inserts varies a lot. However, while maintaining the desired application purpose, service life, and production cost of the mold, we can find the general design principles as follows:

1). Insert design should facilitate machining;
2). The mold is easily vented;
3). Mold insert design should help reduce costs and improve efficiency.
3. Fixation and anti-rotation design of inserts
During the insert design process, insert fixationand anti-rotation are also important issues for designers to consider. The common fixation and anti-rotation designs of inserts are shown below (see Fig. 6-9):
(1). Fixed by screws and pins (Fig. 6).
(2). Fixed by stepped pins (Fig. 7).
(3). Fixed by dual cylindrical surface (Fig. 8).
(4). Fixed bylock block (Fig. 9).

In a word, along with the continuous development of China’s mold industry, the insert is playing an increasingly important role in mold design. Here, we have listed some common design forms, as well as fixation methods of the insert. However, insert designs are diversified in real-world application, so we must further improve the design according to actual requirements.