I. Advantages of Two-Color Molding:
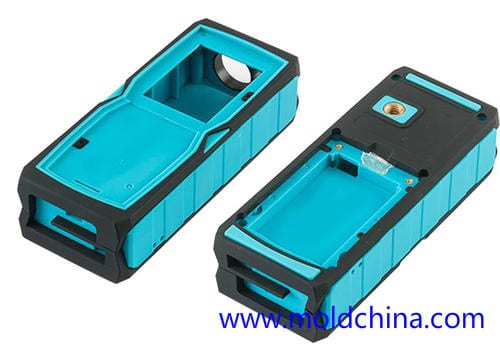
Two-color molding may also be referred to as 2-shot molding, bi-injection molding, co-injection molding, or multi-shot injection molding, which produces a part with two different colors and/or materials in a single operation.
A two-color mold is able to combine two resins with different characteristics and colors into a single two-color product, which reduces the assembly and post-processing of molded products, saves the cost of melting and printing, increases the aesthetic effect, and enhances the grade and added value of the final product, not only anti-skid with increased friction, but also the flexible resin material allows it be more ergonomic with a better feel. A two-color injection molded product features a high quality stability, making it easy to control product deformation, reduce the molding cycle, and increase the output, with a scrap rate 7% lower than that of overmolding, and a product manufacturing cost 20%-30% lower than the latter.
II. How Two-color Molding Works
Two-color injection molding usually refers to the molding of two different types of plastic materials with two different colors. Since the two sets of injection units and nozzles of a two-color injection molding machine are independently separated, the colors of the final products are mostly two-color distinct, without being mixed together. The biggest difference between the two-color injection molding machine and the common injection molding machine is the design of the movable plate of the injection unit. Generally speaking, a two-color machine owns two sets of independent injection units, while a common injection machine owns only one. The configuration of the two sets of injection units varies with the design of each manufacturer. With regard to the design of the movable plate, it is necessary to offer a rotating mechanism. Common designs, such as a turntable or a rotating shaft mechanism are added to provide 180° reciprocation, of which, the rotation function allows the mold to produce cyclical alternating movements. For some specially designed two-color molds, there is no need for a turntable or a shaft mechanism, but the mold itself is able to perform alternate sliding or horizontal rotation.
III. Production Process Characteristics of Two-color Injection Molded Products
1. A two-color injection molding machine is composed of two sets of plastic injection devices with exactly the same structure and specs. The nozzle needs to have a special structure according to the production method, or be equipped with two sets of injection molds with the same structure that is able to be rotated and transposed. During plasticization, the process parameters such as melt temperature, injection pressure, and injection volume in the two sets of plasticizing devices are required to be the same, so the fluctuation of process parameters in the two sets of devices should be minimized.
2. Compared with the common plastic injection molded products, two-color injection molded ones possess higher parameter values for the melt temperature and injection pressure during the injection process, of which the main reason is that the runner in a two-color mold is longer, the structure is more complex, and the melt flow resistance is larger.
3. Two-color plastic injection molded products preferably select raw materials with great thermal stability and low melt viscosity, so as to avoid decomposition due to high melt temperature and long residence time in the runner. The most widely used plastics are PC, PS, ABS, etc.
4. During the injection molding process of two-color plastic products, to make the two melts of different colors well welded in the mold and ensure the quality of the molded products, a higher melt temperature, mold temperature, injection pressure and injection speed should be adopted.
IV. Structural Form of Two-color Mold
There are two forms of traditional two-color injection molds – “Core Side Translation” and “Core Side Rotation”.
1. A “core side translation” mold features two cavity sides and one core sides. When the first barrel shots, the core side closes with the first cavity side, to complete the injection of the first plastic material. After the first plastic solidifies, the core and cavity are separated, and the semi-finished product formed by the first plastic material stays in the core, and moves with it to the location aligned with the second cavity side. After the injection molding machine closes, the second barrel injects the second plastic material. After the second plastic material solidifies, the injection molding machine opens the mold to eject the complete product.
2. A “core side rotation” two-color mold features two cavity sides and a back-to-back core side that is able to rotate. Equipped with two injection molding machines with two barrels, it is better for the second barrel to be designed in the vertical direction to the molding machine movement. Two different plastics can be injected at the same time. When the two injected plastic materials are solidified, the injection molding machine opens to automatically eject the complete product. After product ejection, the “rotatable core side” rotates 180 degrees, and the injection molding machine closes to start the next molding cycle.
Since the first and second barrels in the “core side translation” mold shot in turn, and those in the “core side rotation” mold shot concurrently, with regard to the same product, the production efficiency of the “core side rotation” mold is twice that of the “core side translation” mold.
V. New Technology of Two-color Mold
A two-color injection molding machine is equipped with two barrels. The mold is single-cavity, and possesses a shared cavity required by the first plastic (“hard rubber”) and the second plastic (“soft rubber”). This technology requires a single core and a single cavity, which is fundamentally different from the previous two production modes. After injecting the first plastic into the first barrel, wait for the first plastic to partially or fully solidify, and the hydraulic power cylinder at the beginning of the control drives the isolating blade to retract to be level with the profile of the core. At this point time, the second barrel shots the second plastic. After the second plastic completely solidifies, the injection molding machine opens to eject the complete product. Then, the injection molding machine closes and the next molding cycle begins. The apparent advantage of this technology is that it simplifies the mold and reduces the working space needed by the injection molding machine (a smaller two-color injection molding machine can be used to reduce investment and energy consumption). And, it is able to double the output when compared with the previously used “overmolding” process, while fundamentally avoiding product defects, since the shrunk and deformed “hard rubber” doesn’t have to be placed in the cavity again.
VI. Difference between Overmolding and Two-color Molding:
1. Two-color molding: The two plastic materials are injected by the same injection molding machine and shot twice, but the product is only ejected once. Usually, this molding process is also referred to as two-shot injection, which is usually completed by a set of molds and requires a special purpose two-color injection molding machine. A two-color mold is able to combine two resins with different characteristics and colors into a single two-color product, which reduces the assembly and post-processing of molded products, saves the cost of melting and printing, increases the aesthetic effect, and enhances the grade and added value of the final product, not only anti-skid with increased friction, but also the flexible resin material allows it be more ergonomic with a better feel. A two-color injection molded product features a high quality stability, making it easy to control product deformation, reduce the molding cycle, and increase the output, with a scrap rate 7% lower than that of overmolding, and a product manufacturing cost 20%-30% lower than the latter.
2. Overmolding (two-stage molding): The two plastic materials are not necessarily injected by the same injection molding machine, but are molded in two stages; after the product is taken out from one set of molds, it is then put into another set of molds for the second stage injection molding. Therefore, this type of molding process is usually completed by two sets of molds, without the need for a special two-color injection molding machine. The mold structure is the same as that of the single-color injection mold, but the injection parameter – the flow rate is mainly adjusted to control the binding point of the two materials. Overmolding mainly involves the soft rubber encapsulating the hard rubber, among which the soft rubber usually includes artificial rubber, TPU and TPR, while the hard rubber can be ABS, PC, PP, etc.