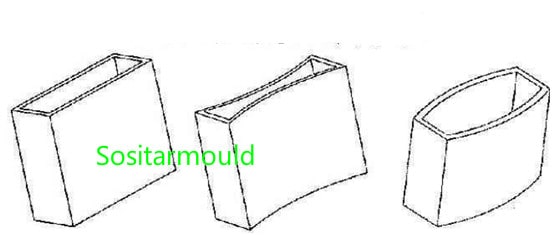
Warpage refers to the deviation in the shape of a plastic injection molded product from the shape of the mold cavity, as shown in the figure. It is one of the commonly seen defects of plastic products. The warpage of molded products is affected by many factors – mold structure, thermophysical properties of plastic materials, and the conditions and parameters of the injection molding process all influence the warpage of a molded product to varying degrees.
As people impose higher and higher requirements on the appearance and performance of a plastic product, the degree of warpage, one of the important indicators for evaluating plastic product quality, has also attracted more and more attention.
Warpage Cause Analysis

(1). Unbalanced Molecular Orientation
The warpage of thermoplastics largely depends on the difference between the radial and tangential shrinkage of a plastic product, which is caused by molecular orientation.
Usually, during the injection molding process of a plastic product, the molecular orientation along the melt flow is greater than that along the direction vertical to the flow. This is caused because most of the polymer molecules are arranged along the flow direction during mold filling, while the oriented molecules always try to restore the original curled state, leading to reduction in the length of the plastic product in this direction. Therefore, the shrinkage of a plastic product along the melt flow is greater than that in the direction vertical to flow. Due to the unbalanced shrinkage in the two mutually perpendicular directions, the plastic product is bound to be warped.
In order to minimize the warpage caused by the difference in molecular orientation, conditions should be created to reduce flow orientation and ease the relaxation of orientation stress. Among all, the most effective way is to lower melt temperature and mold temperature. When opting for this method, it is better to combine it with the heat treatment of the plastic product. Otherwise, the effect of reducing the difference in molecular orientation often becomes temporary, because when material temperature and mold temperature are lower, the melt cools more quickly, so a higher internal stress remains in the plastic product, which causes the product to warp during future application or when the ambient temperature rises.
If a plastic product is heat-treated immediately after product ejection, keeping it at a higher temperature for a certain period of time and then slowly cooling it to room temperature is able to largely eliminate the orientation stress in the product. The heat treatment process is: immediately after the plastic product is ejected, put it in 37.5-43°C warm water and allow it to cool slowly.
(2). Improper Cooling
If the mold cooling system is not properly designed or the mold temperature is not properly controlled, insufficient cooling of a plastic product will cause it to warp. Especially, when the wall thickness of it differs greatly, the plastic product is particularly prone to warpage due to inconsistent cooling shrinkage of each part of the plastic product. Therefore, when designing the shape and structure of a plastic product, the section thickness of each part should be as consistent as possible.
In addition, a plastic product must be kept in the mold for sufficient cooling and setting time. For example, rigid polyvinyl chloride (PVC) features a low thermal conductivity. If the central part of a plastic product is not completely cooled before it is ejected, the heat in the central part of the plastic product will be transferred to the outside, which will soften and warp the plastic product.
With regard to mold temperature control, the temperature difference between the mold core and the mold cavity, the mold core and the mold wall, and the mold wall and the insert, should be determined according to the structural characteristics of the molded product, so that the unfavorable orientation shrinkage difference can be offset by controlling the difference in shrinkage speed of each part of the mold, thus avoiding warpage of plastic products caused by orientation. For plastic products with a completely symmetrical structure, the mold temperature should accordingly be kept consistent, so that the cooling of each part of the plastic product is balanced.
What’s worth mentioning is that when controlling the temperature difference between the mold core and the mold wall, if the temperature of the mold core is higher, the plastic product will bend in the direction of the mold core after being ejected. For example, when producing frame-shaped plastic products, if the mold core temperature is higher than the cavity temperature, the frame edge of the plastic product will bend to the inside after being ejected. Especially, when the material temperature is low, the bending phenomenon is more serious due to the higher shrinkage in the melt flow direction. It should also be noted that the mold core is easy to be overheated, so it must be properly cooled. When the temperature of the mold core is reluctant to drop, appropriately raising the temperature of the cavity is also a supportive method.
For the design of the mold cooling system, it must be noted that the cooling channels should be located where the temperature easily rises and the heat is relatively concentrated. For those easily cooled locations, slow cooling should be performed as much as possible to ensure uniform cooling for all parts of a plastic product. Usually, the cavity and core of a mold should be cooled separately, and the distance between the cooling hole and the cavity should be kept moderate, neither too far nor too close, usually between 15mm to 25mm; the diameter of the cooling channel should be greater than 8mm, while the depth of the cooling hole should not be too shallow, the inner diameter of the cooling channel and the joint should be equal to that of the cooling hole, the coolant flow in the cooling hole should be turbulent, the flow rate should be controlled within 0.6-1.0m/s, and the total length of the cooling hole should be kept within 1.2-1.5m or less, otherwise high pressure loss will be caused; the temperature difference between the inlet and outlet of the coolant should not be too great. Especially, for multi-cavity molds, the temperature difference should be controlled within 2°C.
(3). Improper Mold Gating System Design
The structural parameters of the mold gating system are important factors that affect the shape and size of a plastic product. Especially, the mold gate design involves the flow characteristics of the melt in the mold, as well as the formation of internal stress and the thermal shrinkage of the plastic product. If gate location and type are reasonably determined, warpage of the plastic product can often be minimized. When determining gate location, do not allow the melt to directly impact the core, but ensure a uniform force on both sides of the core; for large-sized rectangular and flat plastic products, if resin materials with high molecular orientation and shrinkage are used, adopt film gate or multi-point side gate, and avoid direct gate or pinpoint gate distributed in a straight line; for disc-shaped plastic products, adopt pinpoint gate or direct gate, and avoid side gate; for ring-shaped plastic products, adopt disc gate or ring gate, and avoid side gate or pinpoint gate; for shell-shaped plastic products, adopt direct gate, and avoid side gate.
Besides, when designing mold gating system, the melt flow characteristics should be adjusted to keep the flow as parallel as possible during the mold filling process. This way, large warpage will not be caused, though the shrinkage of a molded product differs in the two mutually perpendicular directions.
(4). Improper Mold Release & Venting System Design
If a plastic product is subjected to a large unbalanced external force during the ejection process, its shape and structure will be greatly deformed, e.g., insufficient draft angle of the mold cavity, difficult product ejection, undersized ejection area or unevenly distributed ejectors, inconsistent ejection speed of each part of the plastic product, or too fast / slow ejection during mold release, improper setting of mold core-pulling devices and inserts, core bending or insufficient mold strength, poor accuracy, unreliable positioning, etc. are all factors that cause warpage to the plastic product.
Therefore, in terms of mold design, the draft angle, and the location and quantity of ejector pins should be reasonably determined to improve the strength and positioning accuracy of the mold; for small and medium-sized molds, anti-warpage molds are able to be designed and produced according to the pattern of the warpage – design the cavity with a curved surface opposite to the warping direction, to offset the orientation deformation. However, this method is difficult to control and requires repeated trial production and mold repair. Usually, it is applied to plastic products with a large quantity.
In terms of mold operation, the ejection speed should be appropriately slowed down or the ejection stroke appropriately increased.
In addition, poor mold venting also has a certain impact on the warpage of plastic products, which should be taken into consideration. Plastic products that are prone to warpage can be placed in wooden fixtures suitable for their appearance and structure to forcibly keep them in shape. However, it should be noted that no pressure should be applied to the plastic product in the fixture, but it should be allowed to shrink freely. Appropriate cooling can be applied to supplement the shaping of a plastic product at the earliest possible time; for box-like plastic products such as turnover boxes, support plates or frames can be used to shape them to prevent their shrinkage or expansion.
(5). Improper Process Operations
During process operation, a plastic product tends to warp if the injection pressure is too low, the injection speed is too slow, the holding time and injection cycle are too short on condition that the mold is not overly filled, the melt plasticization is not uniform, the temperature is too high during the drying of raw materials, or the annealing process of the plastic product is not properly controlled. In this regard, corresponding process parameters should be adjusted separately according to the specific situation.
Warpage Troubleshooting Solutions:

(1). Mold temperature is too high or cooling is insufficient. The mold temperature should be appropriately lowered or the cooling time appropriately extended. Slender plastic products can be cooled after being fixed by clamps.
(2). Uneven cooling. The mold cooling system should be improved to ensure uniform cooling of plastic products.
(3). Improper gate type. A proper gate type should be selected according to the specific situation. In general, the multi-point gate can be adopted.
(4). Eccentric mold. The mold should be checked and corrected.