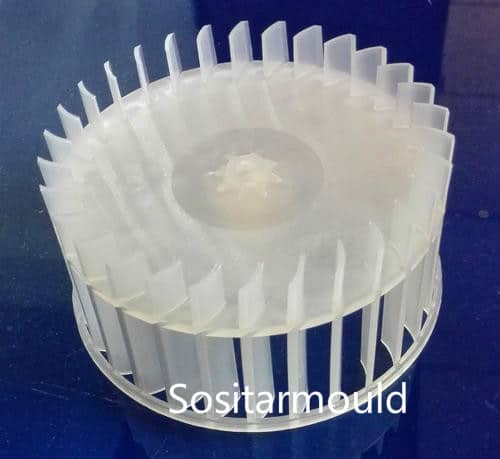
The wall thickness of a plastic injection molded product greatly influences its quality. If the wall thickness is too small, it will be difficult to meet the requirements for strength and rigidity, and fill the cavity for large and complex products; if the thickness is too large, it not only wastes the raw material, but also easily generates bubbles inside the plastic product, while producing defects such as depressions on product appearance. At the same time, it will also increase the cooling time. Therefore, it is important to thin a plastic product from the economic point of view.
When designing a plastic injection mold, it should be considered whether the thickness of the plastic product meets the molding process requirements. If the product is too thin, the flow resistance during injection will be large, the injection molding will be difficult, and sometimes the cavity cannot be fully filled; if the product is too thick, it will not only cause waste of raw materials and increases the molding cycle, but also easily generate such defects as bubbles, dents, and warpage.
Basic principles of wall thickness design:
The wall thickness of a plastic product is required to be as uniform as possible, so as to avoid deformation or cracking caused by inconsistent shrinkage. If the product thickness varies greatly, the product will definitely shrink unevenly during the cooling process, which causes not only bubbles, dents and warpage, but also a large internal stress inside the product, thus affecting product appearance and quality. In actual production, it is difficult to make a completely uniform wall thickness during the design of a plastic product. Usually, it is required that the thickness unevenness of a product does not exceed 50%.
Factors affecting the design of product wall thickness
The basic structure of a plastic product is specified according to the application requirements of the product. The design of product thickness is based on the selected raw material. Therefore, under normal circumstances, when a thick-walled plastic product is designed, two factors, application conditions and plastic manufacturing conditions, should be taken into consideration. Application conditions include: structure, weight, strength, insulating properties; plastic manufacturing conditions include: material fluidity, cooling time, ejection force, as well as assembly strength, dimensional accuracy and more. For details, please see the following 3 points:
1. Structural factors:
The basic structure of a plastic product mainly refers to its shape and size, which is determined according to the application requirements of the product. Since the shrinkage characteristics of plastic during injection molding are different from those of metal, when a metal part is to be replaced with a plastic one, or when a new plastic part is designed, the structure and wall thickness of the metal part must be changed accordingly to make it conform to the principle of wall thickness uniformity of a plastic product. The thick-walled part should be hollowed out and modified to achieve a uniform wall thickness. For example, see the reasonable structural design of several products in Table 1.
Table 1: Examples of reasonable structural design of plastic wall thickness

2. Strength factors:
The strength of a plastic product is determined by the physical and mechanical properties of the raw material under certain structural conditions. Compared with metal, plastic is mechanically weaker, brittle, less resistant to impact, and lighter in weight, so special attention should be paid to the design of plastic product wall thickness to meet the requirements for strength. Although sometimes a product requires very small strength during application, it must withstand the impact and vibration of the ejection mechanism when it is released from the mold cavity, so certain strength against ejection force must be ensured.
3. Plastic fluidity factors:
Plastics possess a certain fluidity after melting in the plastic injection molding process, which varies a lot depending on the different types and grades of the plastic material. Usually, the fluidity of plastics can be tested by the melt flow index (MFI) and the Archimedean spiral flow test. Usually, the higher the melt flow index, the better the fluidity. Therefore, the design of the wall thickness of products of different materials should be as conducive to fluidity as possible, which ensures not only sufficient cavity filling, but also a consistent molten plastic flow speed in all directions, as well as the least resistance in the flow direction. For plastics with great fluidity such as Nylon, PE and PP, the wall can be designed to be thinner. For plastics with poor fluidity, such as PC and PSF, the wall thickness can be designed to be thicker.
Commonly adopted wall thickness of various plastics
It is recommended that general plastic products adopt a wall thickness of 1-6mm, and the maximum can reach up to 8mm. The most commonly adopted wall thickness is 1.8-3mm, which is dependent on the type and size of the plastic part. Table 2 shows the parameters of commonly used wall thicknesses under various plastic injection molding conditions.
Table 2: Minimum and recommended wall thickness of common thermoplastic parts (mm)
Plastic Material | Min. Thickness | Recommended Thickness of Small-sized Plastic Parts | Recommended Thickness of Mid-sized Plastic Parts | Recommended Thickness of Large-sized Plastic Parts |
PA | 0.45 | 0.75 | 1.60 | 2.40~3.20 |
PE | 0.60 | 1.25 | 1.60 | 2.40~3.20 |
PS | 0.75 | 1.25 | 1.60 | 3.20~5.40 |
PMMA | 0.80 | 1.50 | 2.20 | 4.00~6.50 |
POM | 0.80 | 1.40 | 1.60 | 3.20~5.40 |
PP | 0.85 | 1.45 | 1.75 | 2.40~3.20 |
PC | 0.95 | 1.80 | 2.30 | 3.00~4.50 |
PSF | 0.95 | 1.80 | 2.30 | 3,00~4.50 |
UPVC | 1.15 | 1.60 | 1.80 | 3.20~5.80 |