After the plastic material is heated and plasticized in the injection barrel, the molten plastic flow will be injected into the mold cavity through the sprue and runner system, and finally, take shape after being cooled. This process is defined as plastic injection molding.
The process of plastic injection molding
The plastic injection molding process is mainly comprised of 6 steps, namely Mold Close, filling(injection), pressure holding, cooling, mold opening and ejection, which, as a complete continuous process, directly determine the molding quality of the final product.
Filling (injection)
Filling is the first step in the whole plastic injection molding cycle, of which the time starts when the mold is closed and the injection is completed, until the mold cavity is about 95% filled. Theoretically speaking, the shorter the filling time, the higher the molding efficiency is. However, in real-world production, the molding time (or injection speed) is subject to many conditions.
High-speed filling. High-speed filling is always associated with a high shear rate, causing the viscosity of the plastic to decrease due to the shear thinning effect, which reduces the overall flow resistance; the effect of local viscous heating will also thin the cured layer. As a result, in the flow control stage, the filling behavior is often dependent on the volume to be filled. That is, in the flow control stage, due to the high-speed filling, the shear thinning effect of the melt is often very high, while the cooling effect of the thin wall is not that evident, so the effect of the filling rate prevails.
Low-speed filling. When heat transfer is controlled at a low speed, the shear rate will be low too, but with a high local viscosity and a large flow resistance. Due to the slower filling rate of the thermoplastic and the slower flow, the thermal conduction effect becomes more obvious – heat is quickly taken away by the cold mold wall. In addition to the weaker viscous heating effect, the cured layer is thickened, which further increases the flow resistance in a thinner part.
Pressure Holding
The role of the pressure holding step is to apply a continuous pressure, compact the melt, and increase the density (densification) of the plastic to compensate for material shrinkage. During the pressure holding process, the backpressure is high because the cavity is filled with plastic. In the pressure holding and compacting process, the screw of the plastic injection molding machine is only able to move forward slowly and slightly, while the speed of the melt flow is also very slow. At this point of time, the flow is referred to as packing flow. As the plastic is cooled and solidified by the mold wall, and the melt viscosity increases rapidly during the pressure holding stage, the resistance in the mold cavity is thus very high. In the later stage of pressure holding, the plastic part is gradually formed, with the material density continuing to increase. The pressure holding process must continue until the gate is solidified and sealed.
During the pressure holding stage, the plastic is partially compressible due to the very high pressure. In areas with a high pressure, the plastic is denser with a higher density; in areas with a low pressure, the plastic is looser with a lower density, so plastic density changes with location and time. In the pressure holding process, the melt flow rate is extremely low, so flow no longer dominates, but pressure is the main factor that influences the pressure holding process. During the pressure holding process, the mold cavity is full with plastic. At this point of time, the gradually solidified molten plastic serves as a medium for pressure transfer. The pressure in the mold cavity is transferred to the surface of the mold wall through the plastic material, which tends to open the mold. Therefore, an appropriate mold clamping force is required to keep the mold tightly closed. Under normal circumstances, the overflow will force the mold to slightly open, which will help with mold ventilation; however, if the overflow force is too high, it will easily cause burrs, flashing, and even force the mold open. As a result, when selecting a plastic injection molding machine, a sufficiently high clamping force should be ensured to prevent the overflow, and achieve effective pressure holding.
When performing plastic injection molding in new environmental conditions, we need to consider some new injection molding processes, such as gas-assisted molding, water-assisted molding, and foam injection molding.
Cooling
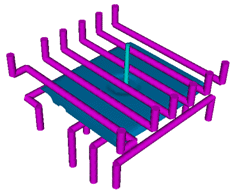
In a plastic injection mold, the design of the cooling system is of great importance, because only after a molded plastic product is cooled and solidified to a certain rigidity, can it withstand the warpage caused by external forces after ejection. Since mold cooling time accounts for about 70% to 80% of the whole molding cycle, a well-designed cooling system is able to greatly reduce the molding time, improve molding productivity, and thus save costs. On the contrary, an improperly designed cooling system will increase the molding time and costs; uneven cooling will further cause warpage and deformation to a plastic product.
Experiment shows that the heat entering the mold via the melt is roughly divided into two parts, 5% of which is transferred to the atmosphere through radiation and convection, while the remaining 95% is conducted from the melt to the mold. Thanks to the effect of the mold cooling channel, heat is transferred from the plastic in the mold cavity to the cooling channel through the mold base via heat conduction, and then taken away by coolant via thermal convection. A small amount of heat that is not taken away by the coolant continues to be conducted in the mold, and then escapes into the air after entering the outside world.
The cycle of the plastic injection molding process is composed of clamping time, filling time, pressure holding time, cooling time and ejection time, among which, cooling time takes up the largest proportion, about 70% to 80%. Therefore, cooling time has a direct influence on cycle length, as well as the production volume of plastic parts. In the ejection step, the temperature of the plastic product should be cooled below its thermal deformation temperature, so as to prevent it from being loosened due to residual stress or warped due to external ejection force.
Ejection
Ejection is the last step in a plastic injection molding cycle. Although the product has been formed and solidified, ejection still has a very important impact on product quality. During ejection, an improper method may cause the product to be unevenly stressed, causing such defects as product deformation. There are mainly two ejection methods: ejector and stripper plate. When designing a mold, you should choose the appropriate ejection method according to the structural characteristics of the product to ensure product quality.
For an ejector-featured mold, the ejectors should be placed as evenly as possible, and locations with the greatest ejection resistance, and where the plastic part strength and rigidity are the highest should be selected, so as not to deform and damage the plastic part.
The stripper plate is generally used for the release of deep-cavity thin-walled containers, as well as transparent products that are not allowed to have ejector marks. This mechanism features a high and uniform ejection force, and smooth movement without obvious marks.
Technical Parameters
Injection Pressure
Injection pressure is provided by the hydraulic system of the injection system. The pressure of the hydraulic cylinder is transferred to the molten plastic through the screw of the plastic injection molding machine. Pushed by the pressure, the molten plastic enters the vertical runner (AKA sprue for some molds), the main runner and the branch runner of the mold through the nozzle of the plastic injection molding machine, and then enters the mold cavity through the mold gate. This process is referred to as the injection process, or the filling process. The pressure is to overcome the flow resistance of the melt, or conversely, the flow resistance needs to be offset by the pressure of the plastic injection molding machine, so as to ensure a smooth filling process.
During the plastic injection molding process, the pressure in the nozzle of the plastic injection molding machine is the highest to overcome the flow resistance throughout the melt. Thereafter, the pressure gradually decreases along the flow direction toward the melt front. If the cavity is well vented, the pressure at the melt front is equivalent to atmospheric pressure.
There are many factors that influence the injection pressure, which can be summarized into three categories: (1) material factors, such as plastic type and viscosity; (2) structural factors, such as the type, number and location of the gating system, the shape of the mold cavity and product thickness, etc.; (3) plastic injection molding process factors.
Injection Time
The injection time mentioned here refers to the time required for the molten plastic to fill up the cavity, excluding the auxiliary time such as mold opening and closing. Although the injection time is short and its impact on the molding cycle is negligible, its adjustment has a great effect on the pressure control of the gate, the runner and the cavity. A proper injection time is helpful for the ideal filling of the melt, and is of great significance for improving the surface quality of the product and reducing dimensional error.
The injection time is much shorter than the cooling time, and is about 1/10 to 1/15 of the latter. This rule can be used as a basis to predict the overall molding time of the plastic part. Mold flow analysis shows that the injection time in the analysis result is only equal to the injection time preset in the process conditions when the melt is completely driven by the screw to fill up the cavity. If the screw pressure is switched to holding pressure before the cavity is filled up, the analysis result will be greater than the preset process conditions.
Injection Temperature
Injection temperature is an important factor that influences the injection pressure. The barrel of the plastic injection molding machine comes with 5 to 6 heating sections, and each raw material has its own appropriate processing temperature (for specific processing temperatures, please refer to the data provided by material supplier). The injection temperature must be controlled within a certain range. If the temperature is too low, the melt will not be plasticized, which will affect the quality of the molded product and increase the difficulty of the process. If the temperature is too high, the raw material will easily decompose. In the actual plastic injection molding process, the injection temperature is often higher than the barrel temperature, which may have something to do with injection speed and material properties, up to 30°C at the most. This is because high heat is generated when the melt is sheared through the gate.
Holding Pressure / Time
When the plastic injection molding process is drawing to an end, the screw stops rotating, but only moves forward. At this time, the plastic injection molding process enters the pressure holding step. During this process, the nozzle of the plastic injection molding machine continuously feeds the cavity to fill up the space created by product shrinkage. If pressure holding is not performed after the cavity is filled up, the product will shrink by about 25%. Especially, shrink marks will occur in areas around ribs due to excessive shrinkage. The holding pressure is usually about 85% of the maximum injection pressure. Of course, it has to be determined on basis of the actual situation.
Backpressure
Backpressure refers to the pressure that the screw needs to overcome when it reverses and retreats to load the material. The application of a high backpressure is beneficial to the distribution of the pigment and the melting of the plastic, but at the same time it increases the screw retraction time, reduces the length of the plastic fiber, and raises the pressure of the plastic injection molding machine. Therefore, backpressure should be set lower, usually no higher than 20% of the injection pressure. When injecting foamed plastic, the backpressure should be higher than the air pressure, otherwise the screw will be pushed out of the barrel. Some plastic injection molding machines come with a programmable backpressure, to compensate for the decrease in screw length during melting, which reduces the heat input and lowers the temperature. However, the result of such changes is difficult to estimate, so it is not easy to make corresponding adjustments to the machine.
What kinds of material we use for plastic injection molding?
It is an important decision for you to choose the proper plastic materials for your project. You have to consider multiple factors before selecting the right plastic materials, such as part application, function, flexibility, durability, and color. Different plastic molding materials look and behave differently, so the materials you choose will have a direct influence on your products’ performance and features. the common plastic we use are as blow:
Acrylonitrile Butadiene Styrene (ABS)
ABS is an amorphous polymer with a density of around 1.05g/cm3. Its overall performance is great, with high mechanical strength, excellent impact resistance, certain surface hardness and anti-abrasion properties. Its heat resistance is as high as 90℃ (even able to be used under the 110 – 115℃ temperature conditions); good low temperature resistance (able to be used under the -40℃ temperature conditions); and allowing easy processing and easy electroplating. But it has poor solvent resistance; easy to age when exposed to UV rays; low extension rate. ABS features a diversity of varieties and an extensive range of applications, so it is also known as “general purpose engineering plastic”. ABS Applications: :Electronic product parts, toys, casings and daily necessities, etc
Polypropylene (PP)
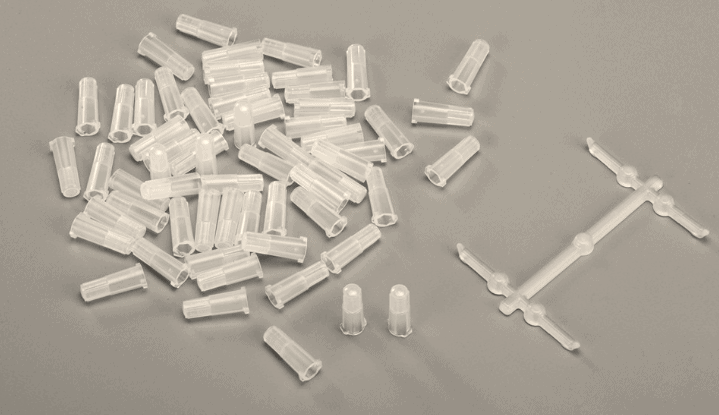
PP is a crystalline polymer, with a density of as low as 0.91g/cm3. Among the commonly used plastics, PP is the lightest; and among all general-purpose plastics, PP is the most thermal resistant – its heat deflection temperature is 80 – 100℃ and can be heated in boiling water.PP features a strong stress crack resistant property and bending fatigue resistance, and it is also commonly known as “polypropene”.PP is lightweight, with good toughness and chemical resistance.but it have some weakness: low dimensional accuracy, insufficient rigidity, poor weatherability. It ages and thus becomes brittle easily. Applications:Various household items, transparent pot covers, chemicals delivery pipelines, chemicals containers, medical supplies, stationery, toys, wires, cups、circulating boxes, pipes and hinges, etc
Polycarbonate (PC)
With a density of 1.2g/cm3 and excellent transparency, It possesses an outstanding overall performance that is characterized by “toughness and rigidity”, with high mechanical strength, great toughness, extremely high resistance to impact, outstanding thermal resistance & weatherability, accurate dimensions and high stability. Besides, it is also non-toxic and odorless.The thermal deformation temperature of PC is between 135 and 143℃, allowing long-term application under the 120 – 130℃ temperature conditions.Its weaknesses: Poor chemical resistance, low fluidity, sensitive to moisture, and prone to internal stress cracks, etc.Applications:High temperature electric products, air blower shells, transformer casings, electric tools, motor casings, tool boxes, milk bottles, beverage dispenser casings, camera parts, safety helmets, gears, food trays, medical devices, ducts, hair pins, hair dressing tools, shoe heels, structurally stronger engineering parts after being fiber reinforced, and CD discs, etc.
Polyamide (PA)
Commonly known as nylon, PA is also a crystalline polymer, with a density of 1.13g/cm3. Among its diversified varieties, the nylon materials that are used for injection molding typically mainly PA6, PA66, PA610, PA11, and PA12. Nylon’s advantages include high mechanical strength, high toughness, as well as fatigue resistance, smooth surface, self lubrication, low abrasion coefficient, resistance to abrasion/heat (allow long-term use below 100℃), corrosion resistance and easy processing, etc.PA weaknesses: easy water absorption, imposing stringent requirements for injection molding, poor dimensional stability, and very hot product upon mold ejection due to the high specific heat. Nylon is mainly used in the automobile, electrical / electronics, transportation, machinery manufacturing, wire / cable / communications, film and daily necessity industries for production of various bearings, gears, circular gears, cams, bevel gears, oil pipelines, oil reservoirs, protective covers, support frames, wheel covers and deflectors
Polyoxymethylene (POM )
POM is a crystalline polymer, with a density of 1.42g/cm3. It features high rigidity, and is also called “Acetal”.It possesses many advantages, like fatigue resistance, abrasion resistance, thermal resistance and impact resistance, etc., with a low frictional coefficient and great self lubricating properties. Its heat deflection temperature is 172℃. POM does not absorb moisture easily, so it maintains excellent dimensional stability in a moist environment, with a shrinkage rate of 2.1%, so it is not easy to control the dimensions during the injection molding process.POM are able to replace most of the nonferrous metals, vehicles, machine tools, instrumental internal components, bearings, fasteners, gears, leaf springs, pipes, delivery belt components, electric boilers, pump shells, grids and tap faucets, etc.
Beside the materials we listed,we also use PMMA,PVC,PET,TPE,PS,HIPS,PPS,PEEK,PE,LDPE,HDPE, etc.
Why Choosing Plastic Injection Molding?
1.The plastic injection molding process is able to be fully automatically high production in a very effective way.it will reduce the unit cost dramatically.
2.The process makes it possible to produce the immensely detailed or complicatedly designed parts. there would be little finishing work needing to be done because the produced parts look extremely finished.it will save second machining cost.
3.There are a wide range of materials in the plastic injection molding process,you can choose one to achieve your requirements or mix different materials for a combined outcome.
4.Very little waste will be produced in the injection molding process, because excessive materials are able to be easily recycled.
The common defects during injection molding production
Flow marks/flow lines
Flow marks/lines refers to the wavy lines or patterns appearing on the surface of the injection molded product. This usually happens when the injection speed is slow, or when the surface layer solidifies faster than resin filling.Solutions :1,Raise the injection speed
It is the most effective method to basically eliminate the flow marks by increasing the injection speed .Slow down surface solidification. it is to increase the mold temperature. In this way, it is, to a certain extent, easier to form a jet flow, thus effectively preventing the occurrence of flow marks.
Burn marks
Burn Marks refers to the blackened edge or corner that is caused on the surface of a injection molding product during the injection molding process. the injection speed has a great influence on it. When the melt is slowly injected into the cavity, the flow state of the melt is laminar; when the injection speed gradually increases to a certain value, the flow state gradually becomes turbulent. turbulent flow conditions are prone to burn marks on the surface, as well as pores inside. As a result, the injection speed should not be too high, and the flow should be controlled in a laminar state. When the mold vents are blocked, or the mold venting capacity or location are not properly designed, the gas trapped in the mold will generate high temperature to burn the resin due to adiabatic compression.
Sink Marks
Sink marks refer to the surface depression caused by resin shrinkage. After the crystalline resin is cooled and solidified, its volume is greatly reduced, which results in the sink mark. Since the shrinkage is basically fixed, and the greater the thickness the higher the shrinkage, the sink mark is usually caused in the thick section of a molded product.
Short Shot
Short shot refers to incomplete filling of a mold cavity which results in the production of an incomplete part due to the insufficient plastic fluidity. The main causes are the inappropriate injection pressure and speed (including excessive pressure loss caused by resistance), or inappropriate injection machines. inappropriate product design , choice of plastic .
Scratches
The scratches (scrape marks)on the appearance of an injection molded product usually occur on such deep-cavity products. When it comes to the scratches on the textured surface, the first thing that comes to the mind of an engineer is that the draft angle on the side of the product is not large enough .Excessive injection pressure and holding pressure are also important causes of scratches on product side walls. Excessive injection pressure creates stress that causes product warpage in the mold. The product may be locally pressed on the side wall, so it is easy to scratch the product side surface during mold ejection.
Flash
Flash, also known as flashing or burrs, mostly occurs between the matching parts of a mold, such as the parting surface of the mold, the sliding part of the slider, the clearance of the insert, and the gap of the ejector, etc. If the flashing is not resolved in a timely manner, it will be further worsened, so that the mold will be pressed to cause local collapses or other permanent damages. The flashing occurring in the clearance of the insert and the gap of the ejector will also cause the product to stick on the mold, thus affecting ejection.
There are other defects such as sprue /parts sticking,warpage,weld line,discoloration.black spots,air pupples ejector pin marks,cracks,etc.please visit our blogs if you want to know detail.